STANDARD & SPECIAL MILLING TOOLS
STANDARD LINES
In modern production the accuracy of the milling process plays a crucial role in the achievement of the requested quality/quantity targets. There are many factors that intervene in determining its growing importance: the reduction of the cycle time and the continuous request for qualitative improvement in terms of roughness, flatness and lift. For these reasons is required the support of instruments with an ever higher performance both in qualitative and quantitative terms, where quality, speed of processing and tool life become essential. The demand for parts with different physical characteristics, extremely rigid in some cases, but also slender and thin in others to meet the needs of lightness of modern industry, bring out the increasing importance of a cutting edge of high quality and versatility of application. The evolution in materials, then, with the adoption of carbon, magnesium, composites, bimetallic alloys, CGI cast irons, tenacious cast irons, in addition to traditional gray cast irons and aluminum alloys, requires equally advanced approaches in processing. The range of cutters offered by IT.TE.DI. allows you to maximize the performance of each process.
-In case of special requests IT.TE.DI. is ready to study special solutions, with specific geometries and PCD grades suitable to the material to machine and to the type of machining.-
The TediMill cutter line is studied to approach operations from roughing to superfinishing, with the internal coolant that goes to the cutting edges through the channels of the cover, a better chip control is ever guarantee during the machining.
Provided with monoblock or shell type body, the TediMill milling line achieve high quality surface with both aluminium and non-ferrous materials.
TEDI MILL cutters in PCD are the best solution to machine aluminium alloys, magnesium alloys, carbon, graphite, bimetallic alloys and generally abrasive materials. The high performance line, the integral mono block types, thanks to its extreme rigidity and the extreme compactness of the body can perform high cutting speeds.
TEDI MILL cutters in CBN are the best solutions to machine grey cast irons, CGI cast irons and hard steels with hardness over HRC 40.
The concept of this milling line has been developed to increase the rigidity and stability of the cutting edge.
TEDI MILL cutters are very versatile: one cutter body may be equipped with inexpensive “disposable” cartaridges or with cartridges that can be retipped several times. There is the additional option to add one or more wiper cartridges to the cutter according to the machining operation.
TEDI MILL cutters are provided with a quick and precise micrometrilac adjustment system which allows to set each individual cartridhes, in order to achieve minimal azial run-out and thus ensure a good surface quality and long life of the cutting edges.
–In case of special requests IT.TE.DI. is ready to study special solutions, with specific geometries and PCD grades suitable to the material to machine and to the type of machining.-
TEDI FEED is the new line of mill with tangential technology available with PCD and CBN inserts with single tip, double tip and full edge cutting edges.
With an high number of effective cutting edges, TEDI FEED is studied for operations from heavy roughing to finishing, reaching high speed machining ( over 2500 m/min )
With internal coolant and axial adjustement, TEDI FEED milling line is available with all kind of holders:
- cylindrical shank.
- monoblock type.
- shell type.
- threaded cofniguration.
TEDI FEED is an high performance mill with tangential inserts, available on HSK, CAT, ISO and BT for the monoblock type, and bi-metal body for the shell type.
Inserts are screw clamped in mill body that in TEDI FEED is provided with or without axial adjustement.
With several combination of insert available is possible to cover a wide range of material and applications: scraper, wiper and full edge.
TEDI FEED cutters are provided with a quick and precise micrometrilac adjustment system which allows to set each individual cartridges, in order to achieve minimal axial run-out and thus ensure a good surface quality and long life of the cutting edges as the Tedi Mill milling line.
-In case of special requests IT.TE.DI. is ready to study special solutions, with specific geometries and PCD grades suitable to the material to machine and to the type of machining.-
The TEDI OCTO CUT is the line with CBN octagonal inserts for grey cast iron parts in high speed processes: it guarantees a better cycle time and long usability of the inserts thanks to their design. When the insert edge is worn, you can rotate it to have a new face ready to work: this operation can be done eight time as per total edges of the insert.
TEDI OCTO CUT are provided wiper inserts to have an high quality surface finish at high feed rates.
The seats of the cutting edges pack (wedge, cartridge and insert) is the same for each pocket, so you can mount different wiper or scraper insert.
TEDI OCTO CUT is studied for operations from roughing to finishing.
The TEDI OCTO CUT milling line is available only with shell type mill and it’s can be used indifferently with standard face milling adaptors or with IT.TE.DI. adaptors.
-In case of special requests IT.TE.DI. is ready to study special solutions, with specific geometries and PCD grades suitable to the material to machine and to the type of machining.-
During a CNC machining the cycle time is very important to improve the productivity: to guarantee it, maintaining a perfect surface finish, we studied the new TEDI S FEED line with a high number of cutting edges.
The main characteristic, due to the high performance during the process, is the maintaining of the rigidity and stability of the mill and of its components. So, to have those aspects with the high number of cutting edges, we developed a special design cutting edge pack.
TEDI S FEED is studied for finishing and superfinishing operations in aluminum components with double clamping for an high rigidity during the process.
Thanks to its features TEDI S FEED achieve the best cycle time machining:
- Suitable for high speed machining.
- Low cutting forces.
- Precise azial adjustment.
- Superior number of cutting edges for high productivity.
- Internal coolant.
With a depth of cut ≤2mm the TEDI S FEED is available with different kind of holders:
- Shell type.
- Monoblock.
- Cylindrical.
-In case of special requests IT.TE.DI. is ready to study special solutions, with specific geometries and PCD grades suitable to the material to machine and to the type of machining.-
The variety of IT.TE.DI. brazed cutters, endmills and integral monoclock, all regrindable, allow a prefect use in a wide range of operations and materials and guarantee excellent perfomrances int erms of quality, consistency and working speed in faceing, interpolating and profiling operations. The studies which have allowed IT.TE.DI. to make variety of extremely flexible brazed cutters, which can be employed immediately in any application. Their structural and technical features, together with the accurate quality inspections thei go through, make the IT.TE.DI. brazed cutters the ideal tool in both roughing and finishing.
Thanks to the high number of cutting edges IT.TE.DI. Brazed PCD mills guarantee an high productivity of the process.
The R&D team of IT.TE.DI. studies the best productive options, the Brazed PCD mills are available with different kind of shape like helicoidal cutting edges to avoid the vibrations and ideal to approach thin structures.
Brazed PCD mills are available in metrical an imperial measurement and with a back end available with HSK, SK and BT holder.
-In case of special requests IT.TE.DI. is ready to study special solutions, with specific geometries and PCD grades suitable to the material to machine and to the type of machining.-
The use of PCD and IT.TE.DI’s avant-garde R&D department solutions allow us to manufacture high performance tools.
Solid PCD mills Micro Line is the best solutions to approach thin structures and thin walls; the parameters of this line of mills guarantee an high productivity of the process.
Available in three type of shape:
- Helicoidal.
- Torus.
- Spherical.
-In case of special requests IT.TE.DI. is ready to study special solutions, with specific geometries and PCD grades suitable to the material to machine and to the type of machining.-
SPECIAL MILLING TOOLS
Our range of PCD and CBN brazed cutters with cylindrical shank and monoblock, all regrindable, can be employed in many different operations and materials with the utmost results, consistent performance and speed, in face milling operations as well as interpolation and scanning.
The study carried out on the different types of machinings and the know-how we have acquired have enabled us to develop a wide range of brazed cutters.
From mirror surfaces to controlled roughness the employment of IT.TE.DI. mills with adjustable or non -adjustable PCD and CBN cutting edges allows to optimize the results in terms of machining times and quality of the surfaces.
Mechanically Clamped Tools
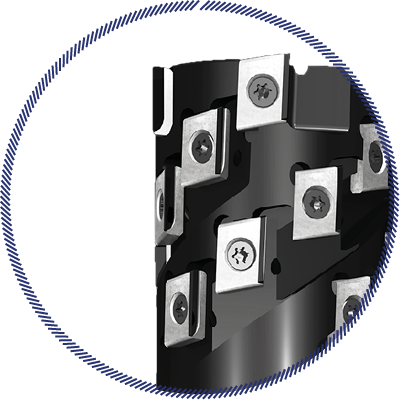
The high technology of the mechanically clamped tools guarantees a loong tool life, thus allowing an high level of productivity. The advantages of this solution lie in the simple adjusting procedure and interchangeability of the cutting edges. The adaptability of IT.TE.DI. tools and the wide choice of standard and special inserts with screw or bracket clamping guarantees escellent results in both roughing and finishing.
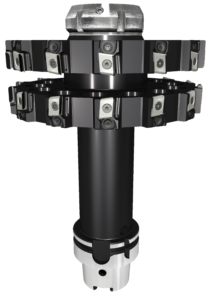
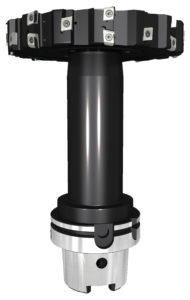
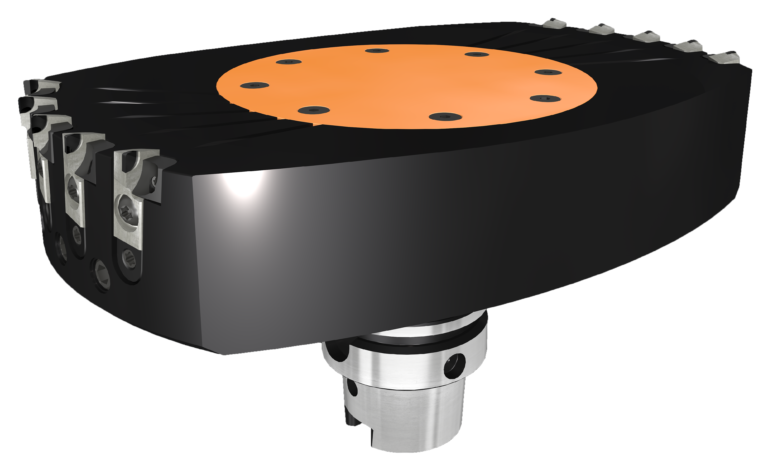
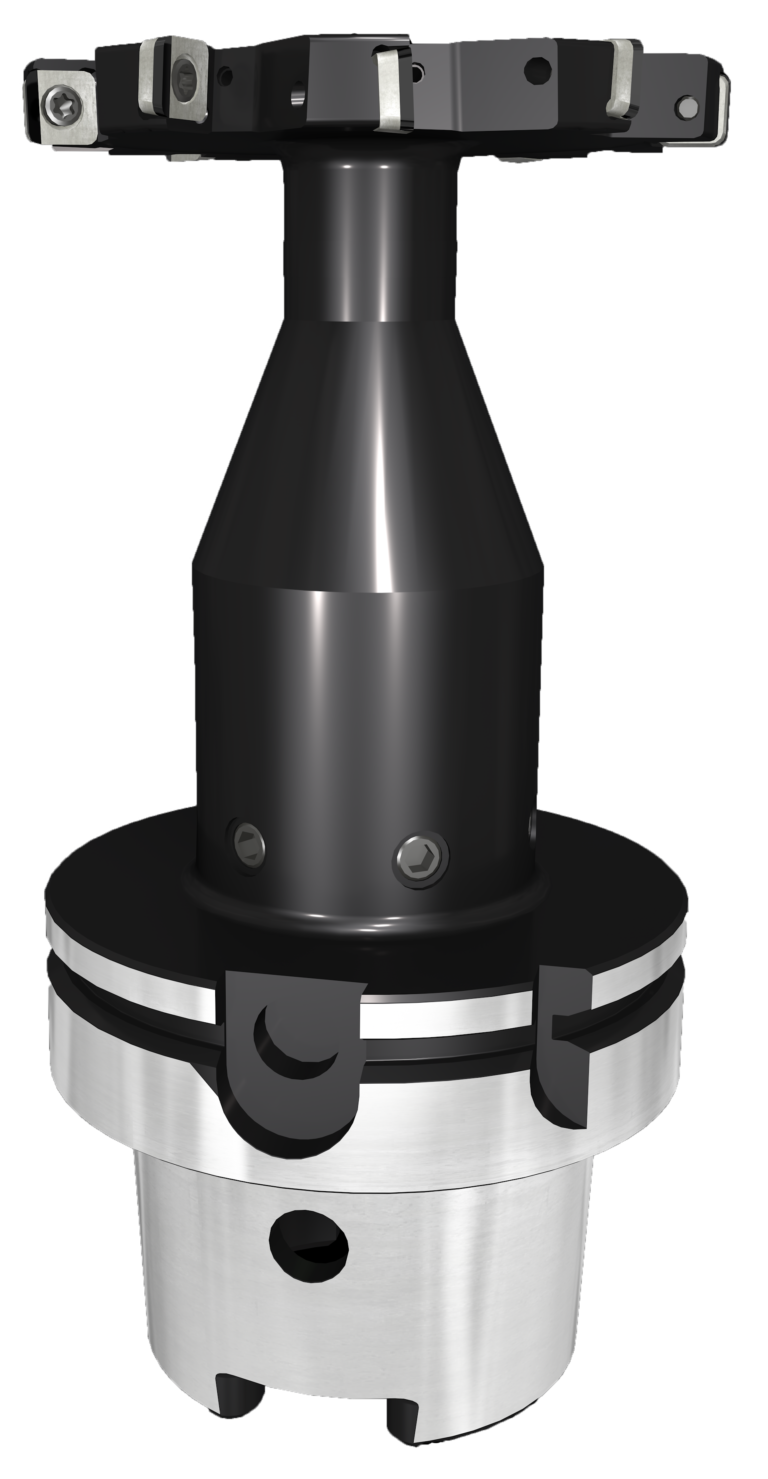
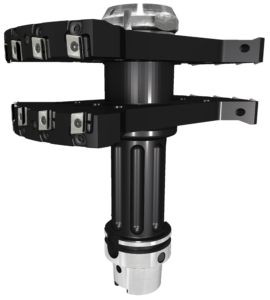
PCD & CBN Brazed Tools
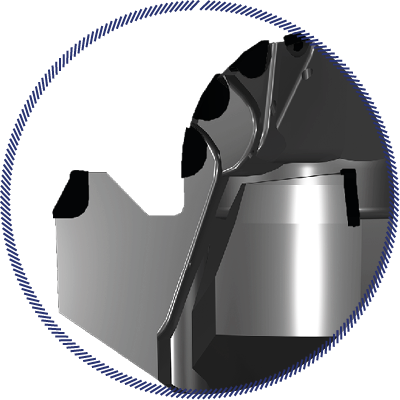
The exclusive grinding system developed by IT.TE.DI. allows the cutting edges of our special PCD and CBN brazed tools to run at high speeds. The manufacturing accuracy and reliability guarantee the maximum perfrormance in terms of tool life and feed while maintaining dimensional accuracu of the piece part.
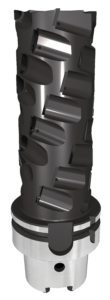
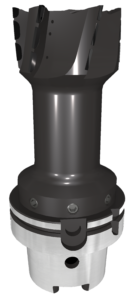
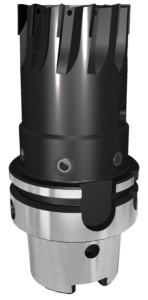
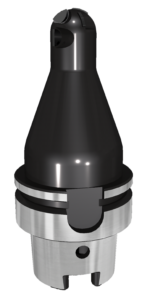
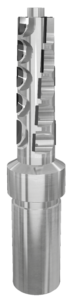